Onion 25 t/h & Shallots 7t/h.
The main purpose of the installation is to process shallots. The shallots are graded over the radial grader. See also example for onion 25 t/h. However, in the setup shown, we expanded the line with a shake grader. The displayed setup is now suitable for processing both shallots, onion sets and regular onions. We have integrated two forms of grading in the line in the setup. The radial grader for shallots and onion sets and the shake grader for regular onions. The regular onions in this region are somewhat flat, which is why a shake grader must be grading by square size. . The shake grader and the radial grader both have five outputs. Processing of shallots, the capacity will vary considerably per batch. A capacity of twenty tons per hour can be achieved with the regular onions. After the onion toppers, the choice can be made for one of the grading machines. The installation is also carried out with a storage / smart hopper block. The whole is a compact installation where as few forklift movements as possible take place.
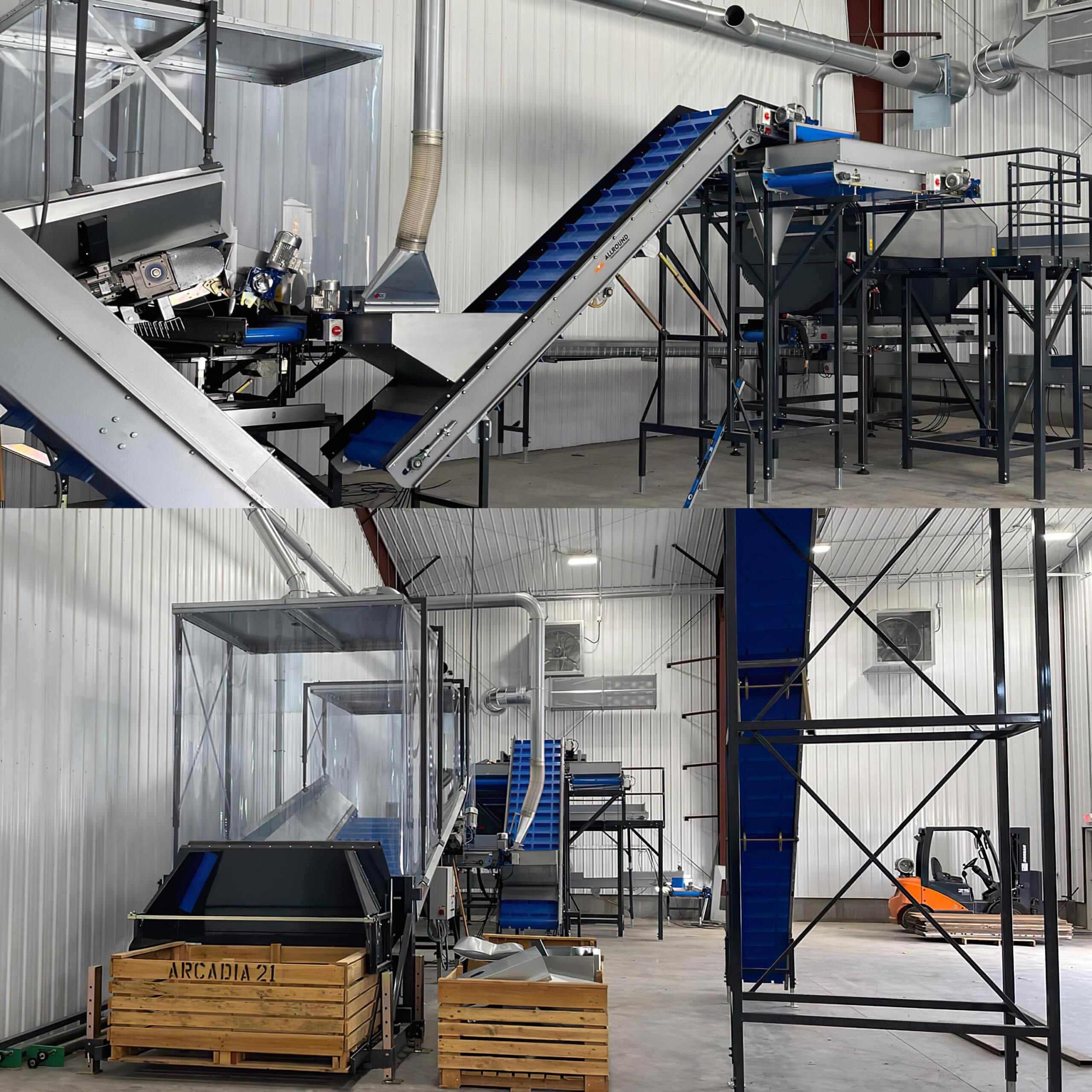
Zone 1 : Receiving area.
The main purpose of the installation is to process shallots. The shallots are graded over the radial grader. See also example for onion 25 t/h. However, in the setup shown, we expanded the line with a shake grader. The displayed setup is now suitable for processing both shallots, onion sets and regular onions. We have integrated two forms of grading in the line in the setup. The radial grader for shallots and onion sets and the shake grader for regular onions. The regular onions in this region are somewhat flat, which is why a shake grader must be grading by square size. . The shake grader and the radial grader both have five outputs. Processing of shallots, the capacity will vary considerably per batch. A capacity of twenty tons per hour can be achieved with the regular onions. After the onion toppers, the choice can be made for one of the grading machines. The installation is also carried out with a storage / smart hopper block. The whole is a compact installation where as few forklift movements as possible take place.
Zone 2 : Grading and Sorting
For grading you can choose from two types of grading machines. The radial grader for the more round varieties and the shake grader for the more flat varieties. After the onion toppers, the onions come on a reversible belt on the right to the radial grader and left to the shake grader. Both grading machines have five grades. It depends on your specific wishes what minimum and maximum size the machines must have. For manual inspection, a flat belt was chosen for both machines. When one has onions with a stronger skin, a roller inspection table is usually chosen. With a roller inspection table, one is more likely to see the entire onion during the selection. The number of storage hoppers is three, the number of outputs on both of the grading machines is five. We therefore have to collect two grades in bins. The grades to be collected in bins will be the under size and over size. With the central operation panel or from the tablet you can determine which grade goes to which storage hopper.
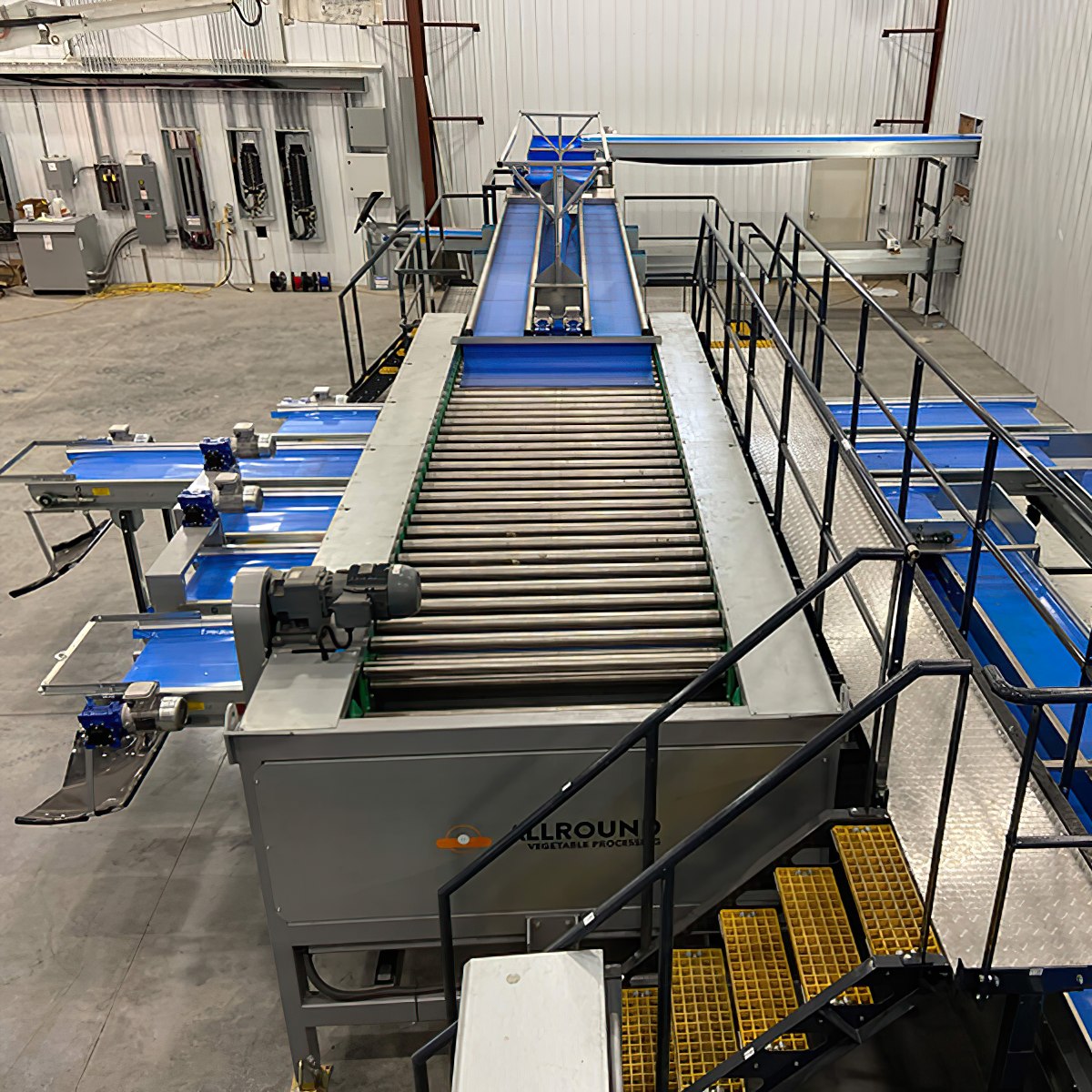
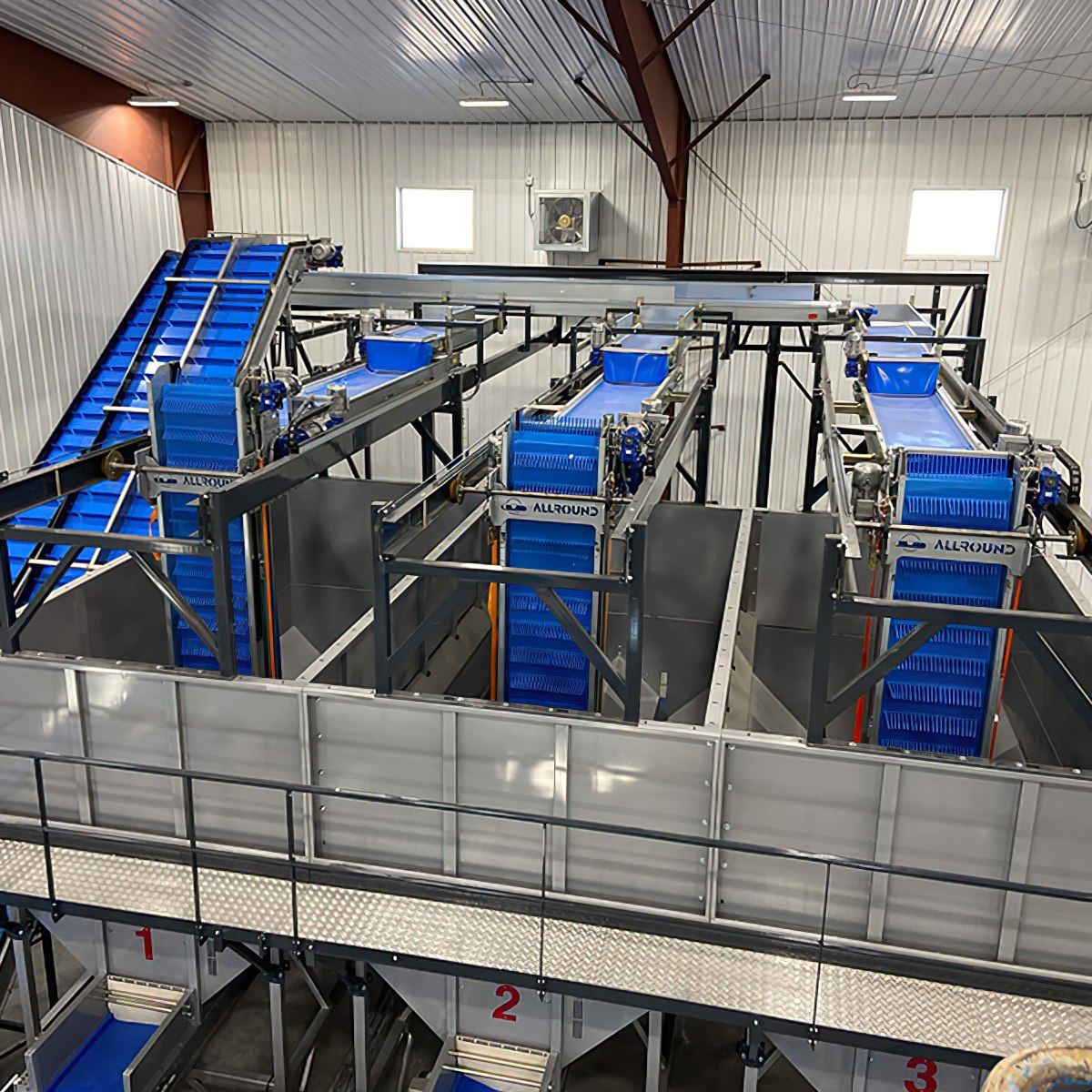
Zone 3 : Storage hoppers and box infeed
After the shake grader or radial grader, the three main sizes are collected in three storage / smart hoppers. Storage / smart hoppers are the most efficient to run your line at 100% capacity all the time. The storage smart hopper is deigned to act as buffer in a processing and a packaging line. The content of the storage hopper depends on the length and the height. The hoppers in this line are a combination of a smart hopper and a storage hopper. The smart hopper is usually longer than a storage hopper. A smart hopper has a less drop height because of the moveable vertical belt which puts the product in the hopper in layers. From the storage / smart hoppers we can unload on two sides. From any storage / smart hoppers you can go to any weighing and packaging machine. Two of the five sizes are collected in cubic boxes. The cubic boxes are aligned with a storage hopper – box tipper combination. With this machine we have a verry space efficient solution to feed the line. ( see website Allround).
Zone 4: Weighing, packing palletizing.
From the storage / smart hoppers you can go to any of the three weighing and packaging machines shown. Consult with Upmann and Inteq which machines these should be
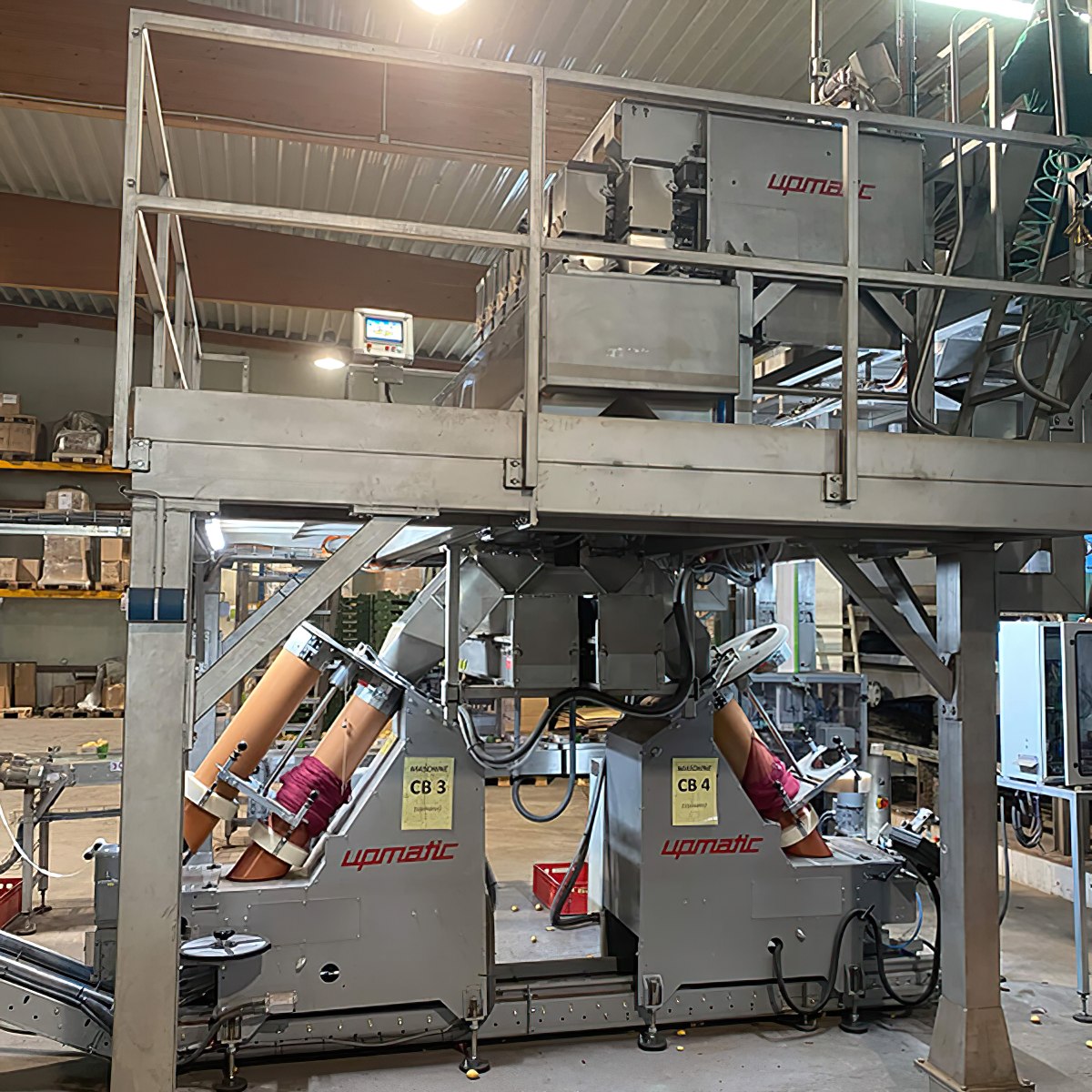