Logistics
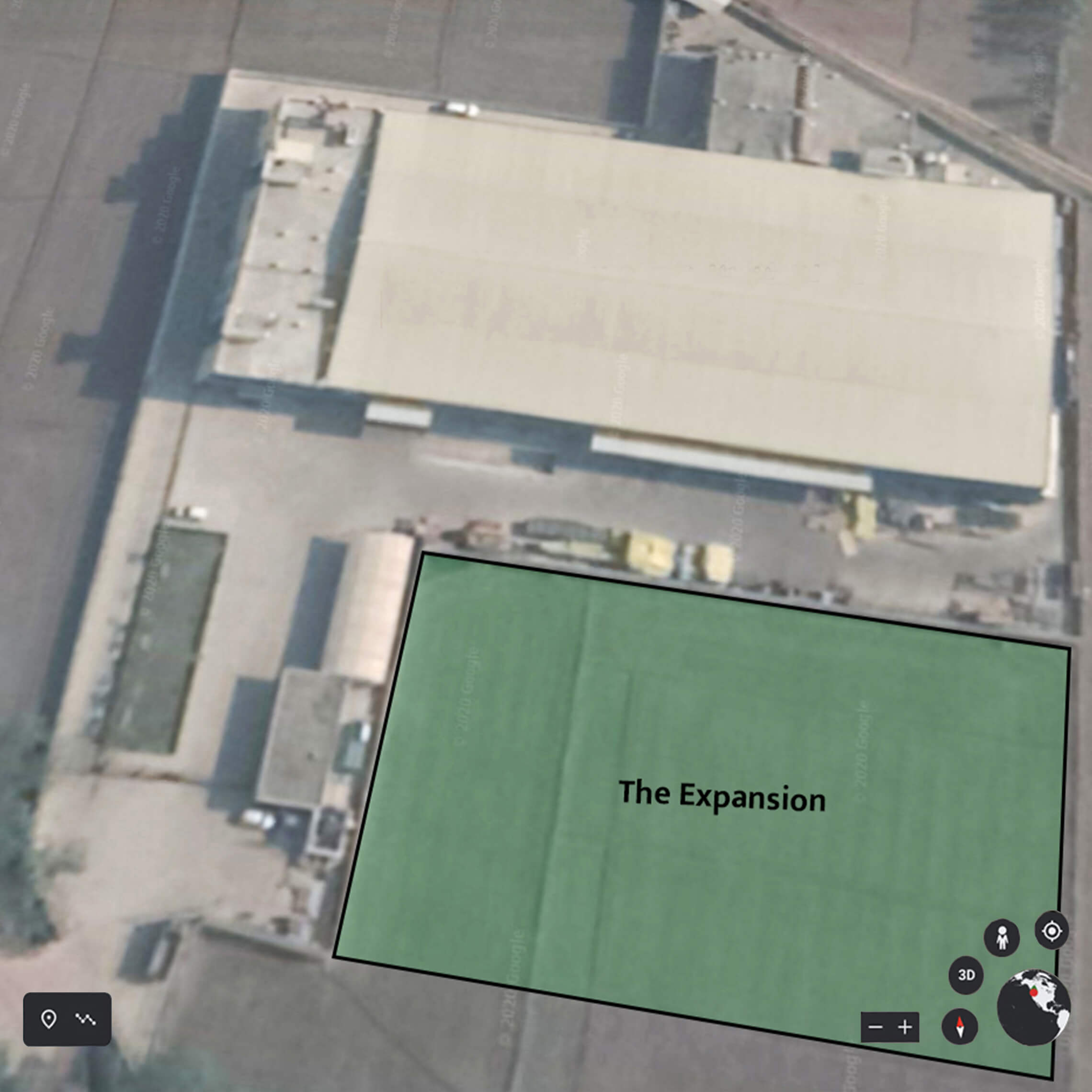
In/out Bond Routing via google earth
At the start of a design of a line or complete installation, we start with a Google Earth picture with the corresponding coordinates. The photo can be of an existing building or of the site on which the new project is to be realized. From this photo the first proposals are made. Important aspects such as the supply of unprocessed product and the disposal of processed product then quickly become clear. At this stage, the possibilities and possible problems for the supply and discharge of water also become clear. Usually the offices and canteen are already designed. This drawing can be used to give other interested parties an idea of your plans. You are then able to give a presentation of your new project at the intended location. The shape of a 3D drawing in the Google Earth photo gives you a very realistic picture. With the first ideas and experience of you and our extensive library of projects in our data base AIMS, we can give you a good picture of your entire project within a very short time.
First in first out, Product and Waste Flowchart
When designing a line, installation or complete greenfield project, we always keep the principle of first in first out in mind as much as possible. It starts with the incoming products. Reception in boxes, tip trailers or trucks then in reception bunkers directly in the processing line or first in storage hoppers. With first in first out, the quality of the product to be delivered remains as high as possible. Product from the receiving bunker in a straight line to the final packaging. In the calculations of the line or installation it is clear where and how long the product must be buffered per grading before it is taken away in retail or whole sale packaging The product may no longer be temporarily stored in boxes when we do not working with an automatic box system. However, when temporary storage is unavoidable, a clear logistics system and routing must be the basis for it. With this system, the first in first out principle also applies. The same principle applies to finished products. The finished product routing should be a logical and straight line. Possibly with roller conveyors for pallets or with a pallet handling system. All sounds obvious but often it isn’t. With the help of 3D drawings, product and waste flow charts, calculations, our large number of examples and your experience, you often come to amazing solutions.
Whole project is divided into different zones.
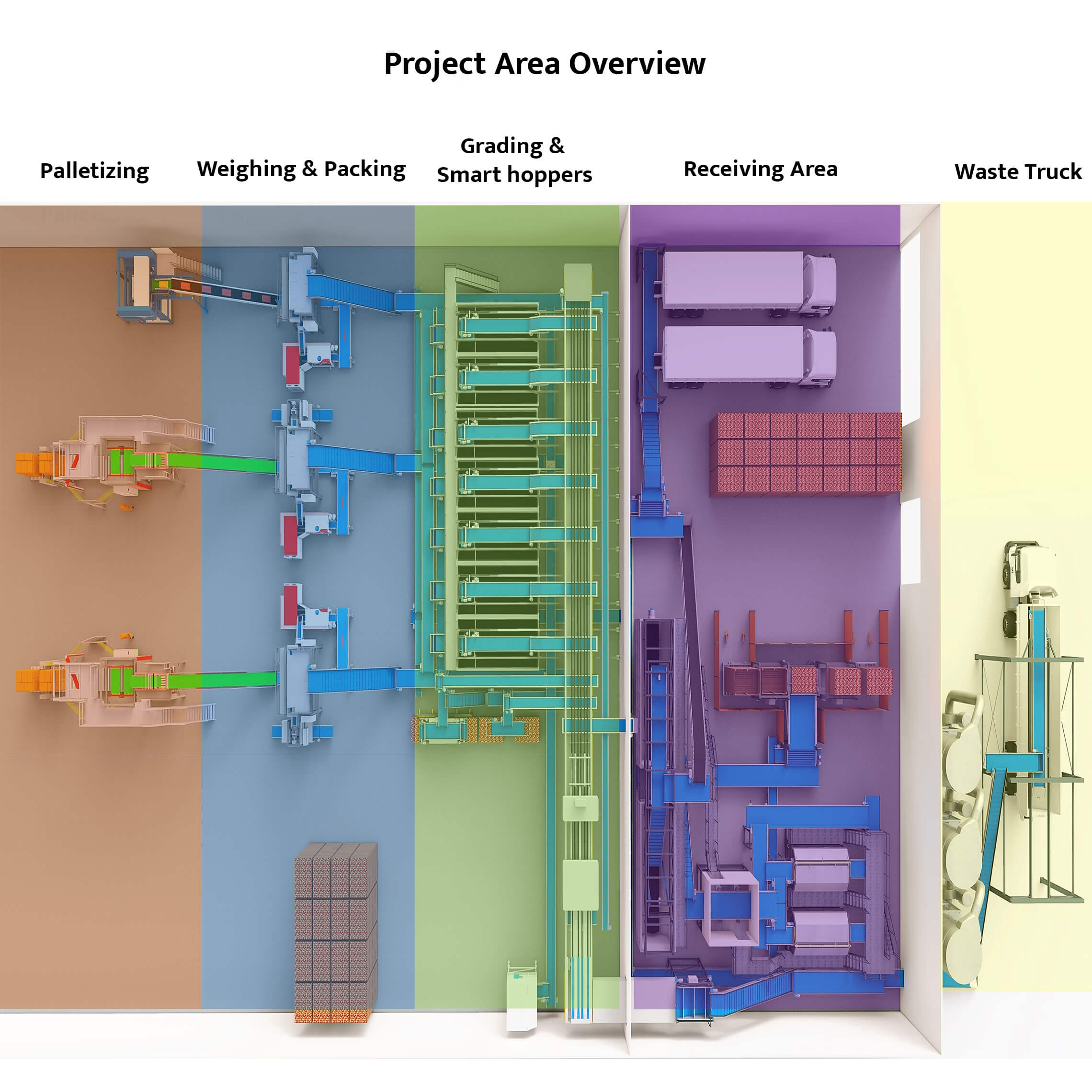
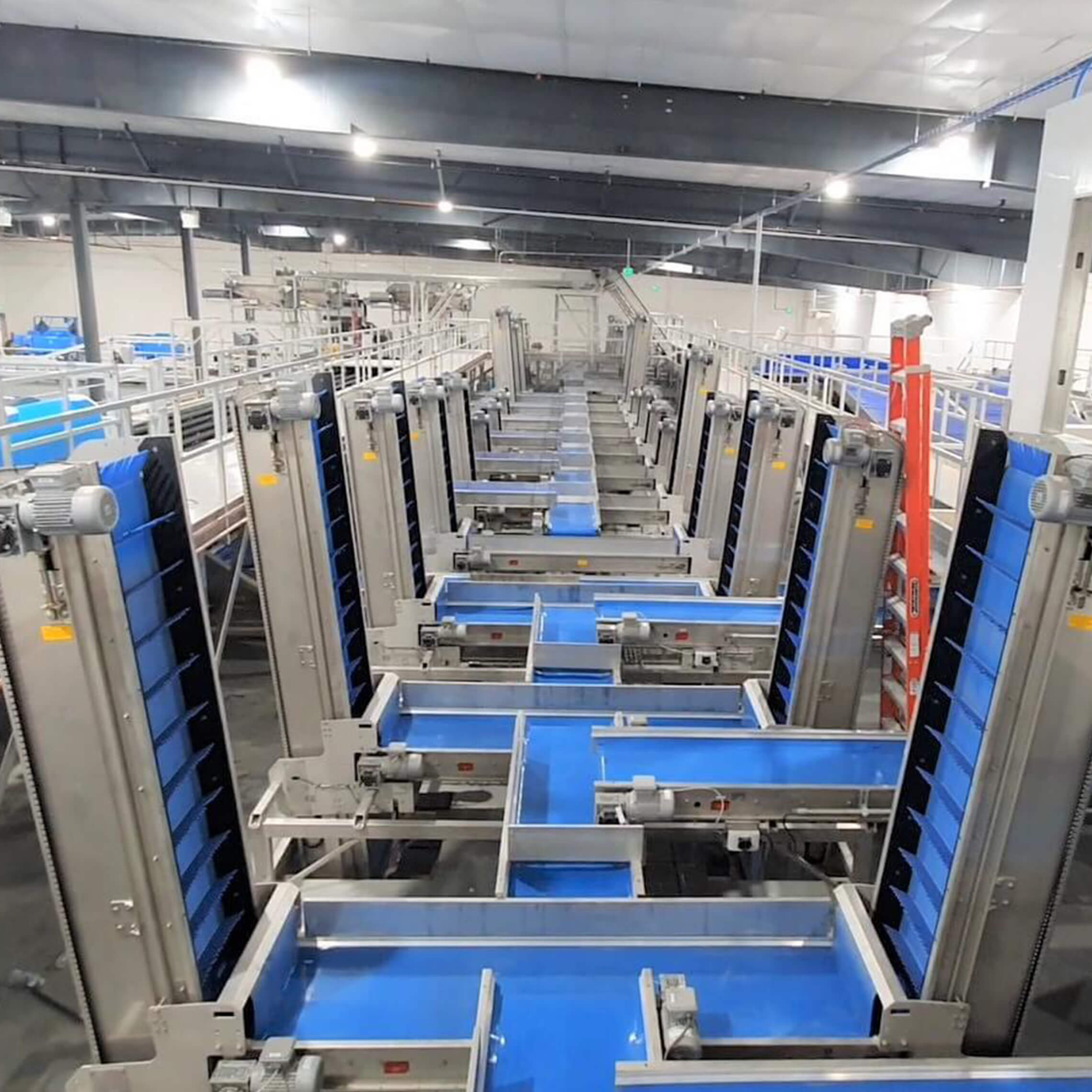
Mezzanine for compact logistic
In many of the projects we have realized in recent years, we have used a mezzanine. A mezzanine is most commonly used for above storage hoppers or smart hoppers. Another possibility is to unload from the mezzanine directly into crates. The most striking advantage of a mezzanine is that you use the ground twice. The product goes up once. Limitation of the number of drop heights. The footprint of the installation remains as limited as possible. A mezzanine or platform with an optical sorter on it is the most common arrangement. An optical sorter with, for example, fourteen sorting turns a batch into fourteen batches. So an optical sorter essentially makes a big mess. With the help of a mezzanine and an automatic box system, storage hoppers or smart hoppers, we turn it into a logical logistics solution. Another application of a mezzanine is that for the storage and supply of packaging material. RPCs are easy to feed to the case packer. You can keep a stock of RPC’s and other packaging material on the mezzanine without interfering with the packaging process. The supply of materials at a mezzanine does not disturb anything either. We can show you many examples with argumentation. The disadvantage is that a mezzanine is relatively expensive.
Finished Retail Product Management
The logistics of packaged potatoes, onions and carrots are an indivisible part of the entire production process. The number of pallets of packaged product is higher than the unprocessed product. The customers increasingly want their own branding. More different packaging with different weights. The delivery times will be shorter and shorter. The logistics process will therefore become more complicated in the future. For complicated problems, you have to find solutions that are as simple as possible. In retail, most products are delivered in RPCs (reusable Plastic Crates) and cartons. Working with a palletizer per packaging machine is the most convenient. This palletizer does not have to be able to do more than palletize the production of this packaging machine. We then select the most cost-effective palletizer. The pallets are automatically collected and placed in the relevant gravity roller conveyor that rolls the pallets at the loading docks. For example, this gravity roller conveyor can be the length of exactly a full truck.
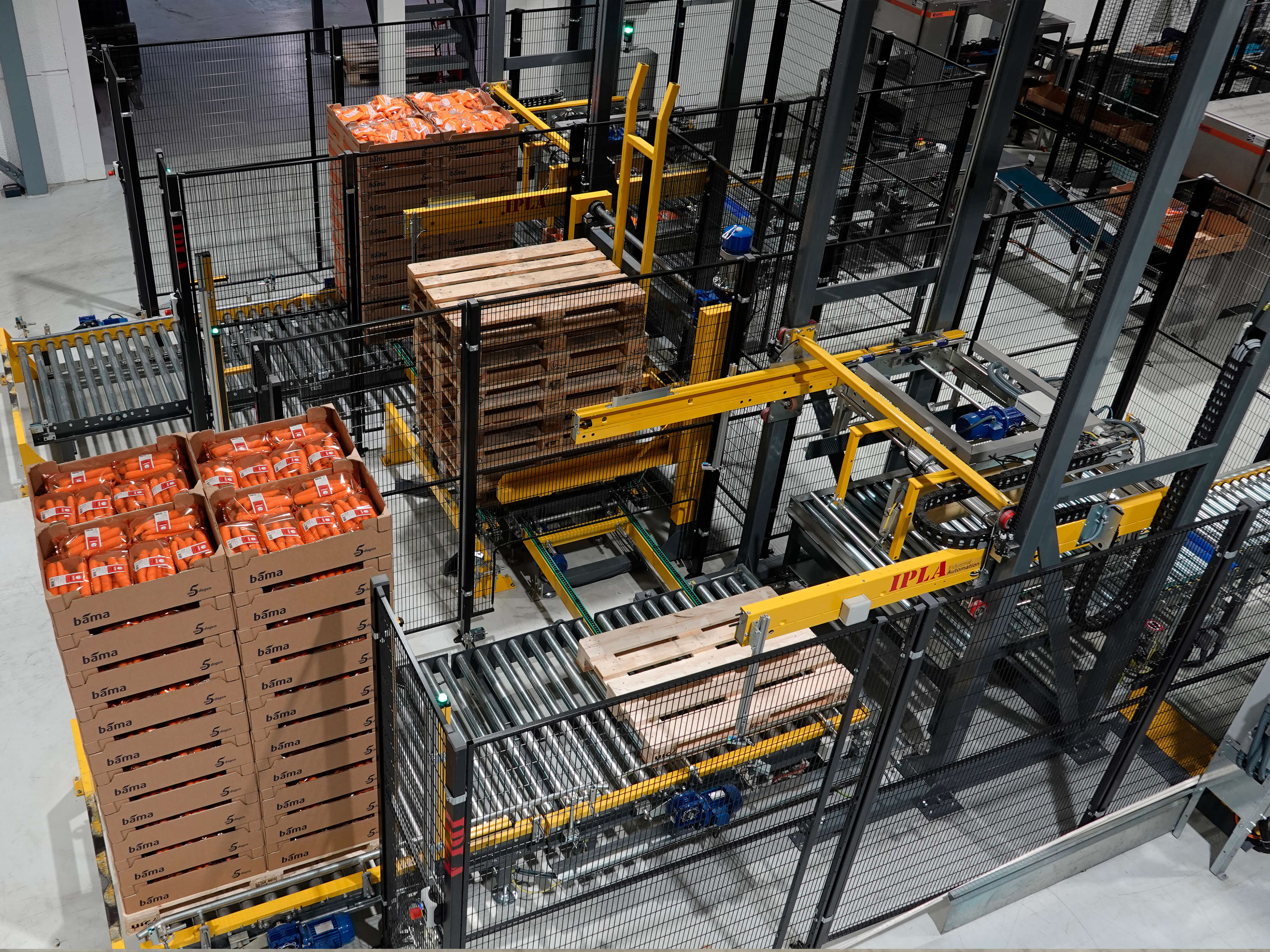